1.
EIFS - A Brief History |
Exterior Insulation and Finish Systems is an
insulating, decorative and protective finish system for exterior walls
that can be installed on any type of construction. It is the only exterior
wall covering that insulates and provides weather protection in a
selection of shapes, colors, and textures that can replicate almost any
architectural style or finish material, or stand by itself as an
architectural finish. While similar in appearance to stucco, EIFS is an
exterior cladding system that consists of components and installation
requirements very different from traditional stucco (see Figure 1 –
Sectional View of a Typical EIFS Application). EIFS also requires very
different care and maintenance than its “look-alike” cousin,
traditional stucco.
In 1952, two significant developments took place
that led to the development of EIFS in Europe. The first patent was
granted for expanded polystyrene (EPS) insulation board and the first
synthetic plaster, an organic plaster using water based binders, was
developed. The use of EPS and synthetic resin materials together began in
the late 1950s and in 1963
|
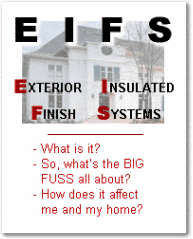
|
EIFS was marketed in
Europe. EIFS answered a need in the European construction market for a
material that could insulate older masonry structures and enhance their
appearance. In Europe, the use of EIFS on stud/sheathing walls is rare, as
most European buildings have solid masonry walls. European concrete or
masonry substrates can function as exterior walls without the EIFS.
European EIFS tend to have thicker and coarser finishes, which provides
for better waterproofing. The systems used in Europe also feature the use
of less portland cement and a higher resin content in the base coat,
giving the system more flexibility and water resistance, albeit at greater
cost.
The
technology for EIFS was transferred to the United States in 1969, when
Rhode Island-based Dryvit Systems, Inc. introduced EIFS in the U.S. During
the oil crisis of the early and mid 1970s, EIFS becomes popular with
energy-conscientious builders and buyers, who sometimes see energy bills
halved. EIFS began by being used almost exclusively in the commercial
building market, and was only gradually adopted for use in homes.
By 1980, EIFS cladding accounted for one-half of 1 percent of the
residential housing market, and by 1995 nearly 200 million square feet
(18,580,608 m2) of EIFS were being installed annually on exterior walls in
North America.
Also,
in 1995, the industry suffered a setback when a number of EIFS clad homes
in the Wilmington, North Carolina area were discovered with moisture
damage behind the cladding. The damage was caused by poor construction
detailing and practices, principally, the omission or improper
installation of flashing in violation of minimum standards of construction
set forth in building codes. A federal and several state class action
lawsuits were filed, only one of which was certified (in the State of
North Carolina). The North Carolina class action was settled by
manufacturers.
While the original problems were discovered first in North
Carolina, it is really a nationwide issue.
In March of 1999, the NAHB (National Association of Home
Builders) Research Center listed the most common problems they found
that were associated with water intrusion in EIF systems as being:
|
The NAHB
commissioned study went on to state: |
|
".
. .homes surveyed ages two to six are experiencing structural damage due
to excessive moisture buildup within walls. The cause of the
moisture accumulation is rain water intrusion from a combination of
factors including: improper sealing at joints and around windows, doors,
and other penetrations; improperly sloped horizontal EIFS surfaces;
inadequate flashing at roof lines, dormers, decks, etc.; and window frames
that leak into wall cavities." |
|
|
|
2. What Is
EIFS (Exterior Insulated Finish Systems)? |
While giving the appearance of
stucco, EIFS is actually a multi-layered wall system that consists of the
following components:
- Insulation
Board - Made of polystyrene (or similar material), which is secured to the
exterior wall surface.
- Base Coat
- Applied on top of the insulation and reinforced with fiber mesh.
- Finish Coat
- Applied on top of the base coat giving a durable, crack-resistant
finish.
The
first half of the acronym, "Exterior Insulation" is derived from
the fact that the first component installed is a foam insulation board.
The foam board is mechanically and/or adhesively attached to the exterior
sheathing of the home. In this respect the foam board serves as an
exterior insulating layer. Over this foam board is applied a synthetic
base-coat material in which is embedded a fiberglass reinforcing mesh.
This is typically referred to as the "base-coat". On top of the
base coat is applied one or more "finish coats". This is the
exterior layer that gives the product its stucco-like appearance. Hence
the second part of the acronym "Finish Systems".
EFIS provides many advantages that other
exterior finishes and sidings do not. Chief among these are superior
energy efficiency and great design flexibility. As a
matter of fact, studies have shown that EIFS can reduce the air
infiltration in a wall by as much as 55%, when compared to standard brick
or wood construction. One should bear in mind that an EIFS system is a
non-structural component of the wall. In other words, it is not
designed to be weight bearing.
Most
early EIFS employed a face
seal
approach
to rainwater management, and was thus very susceptible to failure.
Because of these early problems, most EIFS now incorporates some
sort of a drainage plane to allow for moisture drainage.
Newer installations incorporating this design could be considered concealed
barrier
systems.
However, due to the nature of the product and the realities of the
construction process, even newer drainage EIFS systems can experience
problems:
- “Short-cuts” are often taken in the
application of EIFS systems, causing the primary face seal moisture
barrier to fail and leak (lack of proper caulking, flashing,
etc.).
- The
integrity of the second line of defense is highly dependent on correct
detailing by the designer and proper installation by the builder and
his subcontractors.
Very often, flashings, housewrap, windows, doors, etc., are
improperly installed.
-
EIFS does not breathe and will not allow trapped moisture to evaporate
easily, which can cause great damage over time.
|
Because EIFS (Exterior Insulated Finish Systems)
rely on a perfect seal at the exterior surfaces, they are susceptible to
entrapment of moisture inside the system. Water can enter the system where
seams and seals fail, where moisture migrates from inside the building and
where punched openings (windows, doors, etc.) are present. Because of the
low vapor permeability of the finish, water trapped behind the EIFS cannot
dry out quickly toward the outside of the wall (see figure 1).
Depending on the rest of the wall system design and installation, there
may also be limited drying potential to the inside. Limited drying
potential in combination with high leakage potential can lead to moisture
buildup inside the wall, and eventually to mold growth and structural
decay.
|
|
|
3. The
Causes Of Most EIFS Problems |
Since EIFS clearly provides
many advantages, what's the big deal? The basic problem begins with the erroneous
belief that homes can be made to be “water proof”. The simple truth is, they cannot. For example, even when applied by professional caulking
applicators, All
caulk joints will eventually fail. . . .even those caulk joints made under
laboratory conditions. No
residential windows are fully waterproof. . . .they are designed and
manufactured to a water-resistant standard. Some water will always
find a way in. When it can't
get out, you have a problem.
A. Why Can EIFS Be A Problem?
Homes
clad with EIFS (Exterior Insulation and Finish Systems) a.k.a. synthetic
stucco have a very strong tendency to retain moisture between the
sheathing of the home and the finish system. The design of EIFS, unlike
other systems (brick, stone, siding, etc.), does not allow the moisture to
drain out. The problem is water intrusion and entrapment in the wall
cavities. The moisture can sit in contact with the sheathing for a
prolonged period and rotting may result. Damage can be serious.
While
a brick or stone wall will contain an internal drainage plane behind it
and weep holes along the bottom edge to allow for water drainage, moisture
intruding into the EIFS wall cavities is more damaging because it cannot
readily escape back out through the waterproof EIFS exterior as quickly as
it can through brick veneer, stone, or cement stucco, leaving the internal
sheathing and wood framing vulnerable to rot and decay.
Successful
installation of EIFS
depends upon keeping water out of the wall cavities.
Consequently, in an effort to keep the water out, an industry-wide
installation standard was developed that details installation procedures
to be followed. In conjunction with this, the EIFS manufacturers then trained
and certified applicators to install their products and supplied them with
materials which met specification standards.
But, here is where the system begins to break
down, because unfortunately, the manufacturers failed to take into account
the realities of residential construction:
- Barrier
type systems rarely work.
The EIFS external barrier system depends upon a perfect
external water barrier to keep water out of wall cavities. Since the
outer shell is the only barrier against water intrusion, it must form
a “perfect” barrier at “all times.”
When there are so many entry points for water intrusion in the
exterior shell of a house, this is an unrealistic expectation.
-
Lack
of inspection and enforcement of standards. Most manufacturers, unrealistically expected that the
building industry on its own (including public inspection
departments), would maintain industry standards & specifications,
provide oversight, and provide inspection of the EIF system as it was
installed. Everyone
thought that someone else was minding the store, consequently, the
vast majority of EIFS applications nation-wide, have never been
inspected. Compounding
this problem is the fact that the EIFS manufacturers have failed to
insist upon the very standards they helped originate, be met by the
applicators they supply materials to.
- Evolution
of application guidelines. Another consideration is that guidelines for EIFS
installation have been evolving over the years. An example of this is below grade termination of the EIFS.
While not allowed by building code, early on, it was allowed by
some manufacturers specifications.
However, due to problems with this type of application
nation-wide, in 1996 Dryvit Corp (one of the
largest EIFS manufacturers),
changed all of its specifications to require an 8 inch separation be
left between the EIFS and soil (termite problems in the South &
carpenter ants in the North, moisture wicking up into the EIFS, frost
damage, inability of the EIFS to drain water away if it is buried,
etc.). Unfortunately, this type of new information has been slow to “trickle
down” through the information
chain
(from the manufacturer č distributor č applicator).
Some distributors even claim their insulation-board doesn’t
wick water, and consequently can be placed below grade (experience
shows that it does, however).
- Leaks
and damage are hidden from view. There are few, if any, external visual clues to an
early leakage problem. As a matter of fact, it can take years for an
intermittent leak to evidence itself as damaged sheathing, window
leaks, rotted framing, mold growth, etc.
Many insurance companies, builders, and applicators may not
take a leakage problem seriously, until they can actually see the
damage. The reason
for this “mind-set” is understandable, because no one wants
to be responsible to pay for repairs that may be unnecessary.
Unfortunately, by waiting until a problem is noticeable as
visible damage, the word repair can become the word replace.
What was once a relatively inexpensive repair has become a very
expensive replacement.
- This
is only a "North Carolina" problem.
Wrong, it's a national problem.
It was discovered first in North Carolina.
B.
Problems With Secondary Weather Barrier & Inability To Drain
Most
wood-framed residential homes require a secondary weather barrier to be placed over the sheathing
before the exterior cladding is installed. This barrier protects the home
from incidental water intrusion and allows moisture to exit the home by
traveling on top of the barrier, keeping the sheathing and structural
members relatively dry. Eliminating a barrier and rendering a substrate
unprotected invites trouble, no matter what type of exterior cladding is
used.
Due to the design of the EIFS, a majority of EIFS clad homes
built before 1997 do not have a secondary weather barrier placed over the
exterior sheathing. A large number of EIFS applications use an adhesive to
fasten the two-foot by four-foot insulation boards to the sheathing. If an
adhesive is used to hold the insulation boards to the sheathing, then a
secondary weather barrier cannot be used. Any water that infiltrates the
system will become trapped between the EIFS and the sheathing.
It is estimated that 95 percent of
homes clad with EIFS in the United States are barrier-type. Most barrier
EIFS projects are adhesively applied because it is less time consuming to
install. Adhesively applied EIFS prohibits a vapor barrier from being
installed. It also prevents many self-flashing windows from being
installed properly since the sill flashing must be cut off to accommodate
the adhesively attached foam board.
EIFS
homes built before 1997 have a greater chance for moisture intrusion
problems. Newer EIFS homes built since 1997 using “drainage EIFS” may
have a reduced chance of moisture intrusion, but are not immune.
C.
Lack Of Applicator Training
EIFS
must be purchased from an EIFS distributor. The manufacturer or distributor trains applicators and
issues certificates stating that the applicator has been properly trained.
It is the responsibility of the distributor to ensure that EIFS is sold
only to those certified applicators.
Unfortunately,
certification, training, and insistence upon maintaining standards seems
to have become almost meaningless in the marketplace. For example,
although most every manufacturer requires the use of backer rod &
sealant joints around windows and doors, and edge of the foam should be
backwrapped, these very important details often omitted.
Why?
|

|
Having
said this, still the best way to assure a high quality job is to rely on
members of the EIFS Industry Members Association (EIMA).
EIMA members must meet all applicable building code testing requirements
and industry performance standards.
You
can contact EIMA at 1-800-294-3462, or write EIMA, 3000 Corporate Center
Drive, Suite 270, Morrow, GA 30260.
D.
Deviations
From Installation Guidelines
Deviations
from Industry Standard guidelines during installation,
is likely the largest contributor to EIFS cladding problems.
EIFS application requires the strict observance of manufacturer
recommended specifications and guidelines, and involves meticulous
workmanship and attention to detail. When improperly applied, the EIFS
cladding does not perform its intended function and can allow water to
infiltrate behind the cladding, where it becomes trapped.
Due
to the lessons learned
during the early years of the industry, around 1996 set of
"Installation Details" were developed by EIMA (EIFS Industry
Members Association), that have since become the industry installation
standard. Each manufacturer may have its own specific requirements
as well. EIFS Installation Details are procedures outlined by the EIFS
manufacturer that provide guidance to the architect, builder and
applicator as to the proper installation of the product. All EIFS
manufacturers have details and procedures that builders and applicators
are expected to follow. Installation details are typically very similar
among EIFS products and EIFS manufacturers, but there are differences.
A
common misconception among some applicators is that the “Installation
Details” are designed for specific parts of the country, exposed to
certain weather conditions, and not to them.
This couldn’t be farther from the truth, and has led to some
expensive repairs having to be made. The Installation Details were
designed to be used industry-wide, and are applicable whether the
installation is in a northern cold climate, or southern warm climate. One
should never make the mistake of dismissing as being insignificant, even
some of the smaller deviations from the accepted industry installation
standards. Unfortunately,
there is a long history of applicators having done this in the past. . .to
their great regret later on when the bills come due to pay for replacing
the entire exterior. When
installed properly, many EIF systems can perform well.
However, EIFS is a very unforgiving product and even the smallest
short-cut in installation standards and quality of components, can lead to
big problems down the road.
The
problem we face now is, sometimes an individual contractor may fail to fully
follow the manufacturer's installation guidelines. Often times only
a portion of the guidelines are followed, materials from different
manufacturers are inter-mixed, etc. This can allow moisture into the
wall system. Once the moisture is in it can't get out, which can
lead to wood rot. Some of the
more common installation “short-cuts” are listed below:
-
Foam
insulation placed below grade.
Prior to recent building code changes, the foam board insulation used
in EIFS was placed on the wall below grade. It was discovered that
foam in contact with the ground causes conditions conducive to pest
infestations (termites, carpenter ants, etc.). With EIFS-clad homes,
the visible evidence of infestation is blocked from view by the
exterior siding. In fact, the exterior siding typically looks pristine
and shows no signs of any problems. Behind the EIFS cladding, pests
can live in a protected environment and then establish themselves
inside the home.
-
Another problem
with placing the foam below grade is the ability of water vapor to
migrate upwards through the foam. When the temperature rises at the
transition from masonry to wood, the water vapor condenses and causes
water to settle on the sill plates and exterior band joist. If this
water does not evaporate quickly, wood rot can set in and decay the
structural members of the home.
-
Improperly flashed & caulked windows.
Window leaks account for the
majority of water damage in EIFS houses. The EIFS itself isn't usually
leaking; instead, water is entering between the window and the EIFS,
or the window itself is leaking water. The solution requires a window
flashing that works, as well as a correctly detailed joint between the
window and the EIFS wall. Wherever a window, a door, or an electrical
or plumbing fixture interrupts the EIFS surface, a proper joint must
be constructed, that integrates a reliable flashing into the secondary
weather barrier.
-
A very important component that
is often missing in window detailing is the backer rod.
The backer rod serves two functions: First, it prevents
the caulk bead from adhering to the back of the joint, allowing the
caulk to flex in response to thermal expansion and contraction and
other building movements. If the backer rod is omitted, the caulk will
adhere to the back of the joint as well as the sides, limiting its
ability to stretch and
guaranteeing premature failure. Second, it controls the
thickness of the finished application of caulk, which should ideally
be about half as thick as it is wide. More often than not, though, the
caulk and backer rod are never applied at all.
It is important to keep in mind that no
residential windows are waterproof, they are designed and
manufactured to a water-resistant standard. The very best
windows allow some water into the wall cavity through their own
joints, and “construction grade” windows may leak a great
deal. The quality of windows installed with the EIFS is directly
related to the amount of water that will infiltrate. For example, wood
windows perform poorly, while welded seam vinyl windows perform
substantially better than other window types. EIFS homes cannot be
made totally "water proof", and windows will leak.
Regardless of how well the backer rod/sealant method seals the joints
between window and the edge of the EIFS wall, windows will leak at
some point (even those caulk joints made under laboratory conditions
by EIFS industry engineers will eventually fail).
-
Flashings missing or improperly installed.
are an important element in protecting your house from leakage,
and should be utilized to properly direct water away from the
structure.
Some of the more common locations where they are required are:
deck ledger boards, kick-out flashing at roof / wall intersections, at
window and door heads, headers and other horizontal surfaces, etc.
All too often, flashings are not installed, or installed
improperly.
-
Roof
termination.
EIFS should be held off of roof a minimum of two (2) inches and
backwrapped.
-
Expansion
joints at dissimilar materials.
Expansion-joints should be used where EIFS terminates, or meets a
dissimilar material. The typical expansion joint is a flexible,
watertight joint utilizing, backer rod and sealant. Expansion joints
are typically 1/2 inch in width.
-
Backwrapping.
Where
the foam substrate terminates, it should be backwrapped, in order to
provide for proper protection of the foam. Backwrapping also provides
for improved attachment of the substrate to the sheathing.
-
Horizontal Surfaces: Trim Bands
Quoins. There should be no
horizontal (flat) surfaces. All surfaces should slope away from the
structure.
E.
Divided
Responsibilities
An
EIFS applicator is responsible for the application process-attaching the foam insulation to the
substrate, applying the fiberglass mesh, embedding the fiberglass mesh
with base coat and applying a finish coat. EIFS installers have little
control over construction details designed to prevent water intrusion into
wall cavities from roofs, even including those details which are required
by some state building codes and by the specifications of the EIFS
manufacturers. Many details outlined by manufacturers require the services
of other tradesmen. A typical EIFS applicator does not install backer rods
and sealant, but should install the EIFS so that it is possible to install
these critical components. The builder is responsible for subcontracting
the backer rod and sealant components. Flashing around windows, doors,
decks, chimneys and roofs is the responsibility of the builder and his
roofer. Unless the builder required the roofing subcontractor to install
step flashing and (EIFS required) kickouts, it probably was not done.
The
applicator should recognize improper flashing and not
continue the application process until the problem is corrected.
Unfortunately, this also slows down the overall building process. .
.costing the home builder extra money.
It doesn’t take an applicator long to recognize that an unhappy
home builder may NOT call him to bid on the next project.
According to the National Association of Home Builders Research
Center,
|

|
F.
Pressure
Differentials
EIFS is basically a face-sealed system. The system relies on
a water and airtight seal over the entire wall system. When this is
achieved, an air cavity is created between the exterior sheathing behind
the EIFS and the interior of the home. Positive air pressure changes
caused by wind on the exterior of the home create a negative pressure in
the wall cavity. Any breach in the barrier EIFS system will force air
through that opening and into the wall cavity. When rain is introduced in
this scenario, water (in its liquid form or as vapor), not air, is forced
through any breach in the barrier EIFS. Many researchers indicate that the
difference in pressure differentials is responsible for the majority of
the water intrusions in face-sealed systems. Other wall claddings such as
brick, lap siding, shingles and traditional stucco allow air to
infiltrate, thus rendering the positive force applied to the building to
be balanced.
G.
Lack
of Care and Maintenance
The
beautiful architectural designs made possible by synthetic stucco systems
make these homes very desirable and marketable. It is critical, however,
to carefully maintain these systems to prevent water intrusion and
deterioration. It is very important that the six following steps be
followed to protect your investment.
1.
Annually inspect all sealant
around windows, doors, penetrations through the EIFS, EIFS transitions
(such as EIFS to brick, EIFS to stone), and stucco terminations (at roof,
at grade, at patios or walkways). Arrange for prompt repair of any areas
of caulk that is split, cracking, crazing or is losing adhesion. Also,
promptly repair any cracks in the EIFS.
2.
Any leaks, cracks, areas of
discoloration,
mold or mildew should be promptly investigated by a certified EIFS
inspector. Repairs should be proper and prompt.
3.
Anytime you make a penetration
through the EIFS
such as to mount a satellite dish, add shutters, new wiring, cables,
plumbing, security systems, etc., the perimeters must be sealed with a
quality sealant approved for EIFS.
4.
Modifications, additions or
renovations
(including roof replacement) to the structure of any kind should be
inspected by a qualified EIFS inspector to ensure waterproofing of
critical details is properly performed.
5.
Periodic cleaning of the surface is necessary
to maintain its appearance and prevent permanent staining. Pressure
cleaning equipment must be calibrated to the EIFS manufacturer’s
recommended pressure level (low) to prevent damage. Select a firm with
experience in cleaning these EIFS systems. There are no products that are
totally maintenance free, and EIFS is no different.
6.
Maintenance Schedule. I would recommend setting
up a maintenance schedule with an EIFS specialist to carefully inspect the
exterior for damage, about every 1-2 years.
Any needed repairs should be made at that time (usually just
re-caulking, etc.). EIFS is
the type of system where it is very important to catch any problems
early-on.
In
conjunction with the above noted maintenance schedule, you should contract
with a qualified specialist (i.e. home inspector, etc.), to perform a
complete surface scan of the exterior, on a regular basis (about every 2-3
years or so). This is
performed using a very sophisticated instrument that can detect areas of hidden & trapped moisture beneath the surface of the
EIFS. Again, it is important to catch problems early-on.
|
My own experience in the field,
actually inspecting homes with EIFS, supports the findings of the NAHB
study. I have seen very few homes where the installation
contractor has followed all the industry guidelines and specifications.
This doesn't mean that the EIFS has failed in all these homes. . .it means
that the EIFS is at greater risk of failure and eventual
leakage.
Hire a trained professional to
inspect your house, and give you an assessment as to any needed
repairs.
|
|
Many
times, yes. . .if the problem is caught early. Many homes only require minimal repair (if any at all), in
many cases under $1,000 - 2,000 . Some homes, however, have required
a complete removal of the EIFS, costing thousands of dollars. |
|
Hire a trained professional
to
inspect your house, and give you an assessment as to any needed
repairs. This should be done every year. Start a preventative maintenance program.
Often, only simple caulking will need to be done, and some years nothing
at all. |
|
There is no such
thing as a maintenance free siding material. EIFS is no different,
and will require maintenance and periodic repair on you part. |
|